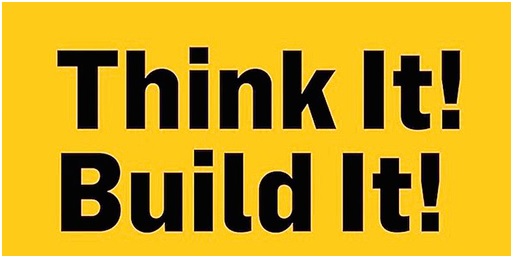
Functional Prototype
Rapid prototyping is a technology that considerably speeds up the iterative product development process. The production line requires a huge capital cost when developing a new product and mold manufacturing also takes quite a long time. A working prototype is needed at the early stage of design for design evaluation and troubleshooting.
Traditionally, it is challenging that design teams have struggled to create ad hoc models that provide an effective basis for specific concepts. This requires almost the same processes, costs, tools, and settings as the final product.
Making prototypes is a risky step for many inventors, designers, and organizations. Furthermore, it can be very difficult to produce a single complicated part with conventional manufacturing operations. While waiting for a prototype to be prepared, facilities and staff still generate costs. In contrast, rapid prototyping provides engineers, designers, and development teams with unique advantages. Time and cost efficiency not only make the team no longer confined to product visualization but can also achieve product functionality.
Functional prototypes are one of the most important steps in the design process. Many companies overlook the need for this simple step due to the cost involved. But the simple reality is that building functional prototypes is much cheaper than direct molding for mass production. It is unwise to go straight to manufacturing by skipping the functional prototype without showing your product features to consumers. Prototyping offers several benefits and you cannot replace them with others.
- Bring Designs to Life: Functional prototypes give you the opportunity to show investors and customers how your products might work. It gives you the opportunity to explore ideas and get some feedback to know how to adjust before actually getting the product to market.
- Select And Evaluate Materials: When you start using materials, you may worry that they won’t work as you expect. Functional prototypes give you an opportunity to understand the performance of certain materials before they execute the final decision. Almost all materials can be used through one or more rapid-prototyping operations. Polymers are the most commonly used material today for workpieces, followed by metals. Moreover, new processes are being introduced continually, and the existing improved process and materials also can better realize the function of the prototype.
- Accelerate Time to Market: In a competitive marketplace, it is well known that introducing a new product earlier than competitors is generally more profitable and can bring a large share of the market. At the same time, there are important concerns regarding the high-quality products to market quickly. Functional prototypes can give you an advantage on time because they can reduce errors and help you better evaluate customers’ ideas for your design.
CNC Prototyping
Rapid-prototyping processes can be classified into three major groups: subtractive, additive, and virtual. As the names imply, subtractive processes involve material removal from a workpiece that is larger than the final part, additive processing builds up a product through adding material incrementally, and virtual prototyping adopts advanced cell-based visualization technologies.
Computerized Numerical Control (CNC) machining is a precision manufacturing process in which pre-programmed can be controlled by a programming language to perform more types of tasks with higher accuracy. Manual control is limited, requiring on-site operators to instruct and guide the processing tool through levers, buttons, and wheels. The CNC process breaks the limitations of manual control and thus replaces manual control. For a layman, the CNC system may just seem like a set of conventional computer components, but the software programs and consoles used in CNC machining distinguish it from that.
Making a prototype traditionally involves a series of processes using a variety of tooling and machines, and typically takes weeks to months according to part complexity and size. This approach requires skilled operators to remove material by machining and finishing operations step by step until the prototype is completed.
To accelerate this process, subtractive processes increasingly use computer-based technologies, such as computer-based drafting packages, interpretation software, and manufacturing software. Prototypes can be produced from a few days to a few weeks. Subtractive systems can take many forms that are similar in approach to the manufacturing cells; Operators may or may not be involved. CNC machining is the most widely used subtractive manufacturing technology and has irreplaceable advantages in functional prototype manufacturing.
Three Advantages for CNC Machining Functional Prototypes
- Material: A wider range of materials can be machined than those that can be applied in the additive process. This is true for metals and plastics.
- Tolerances and Surface Finish: Delivering tight dimensional accuracy and fine finishes are routine for machining. When complex contours/surfaces need to be machined, CNC can provide closer tolerances than manual machines. High tolerances and the variety of surface finish methods both are major advantages of it.
- Low Volume and Short Lead Time: CNC is suitable for one-off jobs and low-to-medium volume production (up to 1000 parts), due to its high repeatability, and it is preferred with fewer paper jobs, and faster prototyping results in very high production and greatly reduced lead times.
No matter what kind of product the company intends to produce, creating prototypes is crucial. Not only the design can be evaluated and tested, but also production costs and problems can be clearer.
Moreover, there is a special situation–when a product needs to apply for a patent. After making a working prototype, it is easier to consult with a patent and see what design aspects may be patentable. Conversely, you also can find out which parts of the prototype and design violate the patents of other individuals and how to change them before production to avoid infringement.